Creating a "WE" Environment to Achieve Safety Excellence
Ever since the mid-eighties, reorganizing, re-engineering, and downsizing have become a way of life. Significant changes and reduction have occurred at every level of most organizations. There are steps you can do to keep your employees from losing their focus in the face of changes.
By: Donald H. Theune, Vice President (Dtheune@topforg.com)
Contents:
The ‘Whys?' of injuries
Core values
Adopting a holistic approach
Defining barriers
Involve all levels of the organization
Steps to Success
RESULTS
Toward Integration
Surveys conducted in the last few years indicate that between 46 percent to 58 percent of employees are 'frequently worried about being laid off.' Between 55 percent to 71 percent of employees "worry a great deal about their company's future." The recent surge of mega-mergers in the petroleum, chemical, pharmaceutical, and pulp and paper industries has dramatically increased the level of stress in the workplace.
This is noteworthy because employees at all levels can lose their focus when put under stress and pressure and reportable accidents and injuries can increase on or off the job. Many managers and supervisors tend to push for increased production in the reorganized, downsized, and/or newly merged companies. As a result, labor and management relations can become more adversarial.
Often, when we ask line employees, "why do injuries occur," they list the following reasons:
- Production/results are Number One.
- When the line goes down, safety goes down.
- Management blames line employees for getting injured.
- Repairs are not made in a timely manner.
- Management doesn't listen to line employees' suggestions.
- Management overlooks unsafe behaviors to boost production.
- Management doesn't "walk the talk."
- The company doesn't care about their employees.
"But we're doing a good job!"
Often when we ask management why employees are getting injured they list the following reasons:
- Line employees take risks and shortcuts.
- Line employees don't follow the procedures.
- Lone employees don't wear their personal protective equipment.
- Line employees have a poor attitude.
- It's the line employee's problem; they have the injuries.
"But we're doing a good job!"
So rather than a "We" environment, we see an entrenched "Us versus Them" adversarial environment; an environment where trust, respect, communication, participation, and cooperation are very limited. These same values are the fundamental building blocks that distinguish a successful company from an unsuccessful one. They also affect revenue, profit, market share, and other measures of success such as production, quality, customer service, and environmental conformance.
Back to top
Once again, here are the core values that present in effective "We" environment:
- Trust
- Respect
- Communication
- Participation
- Cooperation
When these core qualities are in place, the workplace is transformed. It's easier to get things done, whether they relate to production, quality, safety, customer service, or environmental excellence. The company is a nicer place to work because there are fewer obstacles, less bickering, and less stress. Everyone feels valued because they are listened to and treated with dignity and respect. All employees fulfill on their commitment.
Safety is an entry point and an effective rallying point. It is a common ground where both line or labor and management can agree and where they can work together. I have yet to meet an employee who wants to get hurt, a union official that doesn't support safety, or a supervisor who wants to see his or her employees injured.
Companies ask, "How can we overcome the many obstacles to the creation of a ‘We' environment when we are having so much difficulty just reducing accident and injuries?" The answer is simple: Safety, health, and environmental excellence are natural outcomes of a "WE"' culture.
Back to top
A comprehensive and holistic behavioral safety, health, and environmental improvement process implemented by a committed line or labor and management team can help you create a "We" environment. However, there are still some misconceptions held by line employees and labor unions and management that interfere with acceptance and implementation.
First, we have seen members of labor walk out of a behavioral safety presentation over a slide that says, "96 percent of injuries are caused by human error or behavior." When we ask them later why they walked out, they reply that it's unfair to blame workers for all of the injuries. We couldn't agree more! But the slide doesn't say that line employees are the only ones responsible for the injuries.
A comprehensive and holistic behavioral approach says that everyone, line or labor and management, is responsible (not blamed) for the conditions and injuries that occur. Attitude and behavioral change applies to all employees regardless of their position. Ideas for correction, implementation strategies, and committed actions are needed from everyone.
Second, some articles in magazines and chapters in books written by union officials argue that behavior-based safety blames line employees and makes them solely responsible.
It's easy to see why these misconceptions about behavioral safety exist. For many people, behavioral safety is narrowly defined as an observation process where critical behaviors are identified and used to create a "checklist." A relatively small percentage of the workforce is trained to perform these observations on a weekly or monthly basis. Line employees observe other line employees, then provide feedback and record the data for action and analysis.
Any distorted viewpoint could make this look like a "blame the line employee" system. Yet upon closer inspection, we see that identifying and correcting unsafe equipment, processes and procedures is part of the process. Nonetheless, valid questions arise. Is management included in the process? Who trains management on the importance of ‘walking the talk' and being a good role model? How is pushing for production and overlooking risk taking managed and reduced? Are adequate resources allocated to effectively address identified problem areas?
Back to top
In order to select a behavioral process that will have the most powerful impact on your site, we need to define and understand the attitudinal and behavioral barriers that prevent a company from achieving safety, health, and environmental excellence. Closely interconnected barriers, such as an "Us versus Them" attitude, can form a tight web that literally traps a company, stopping progress in the areas of injury prevention, production, quality, customer service, and environmental conformance.
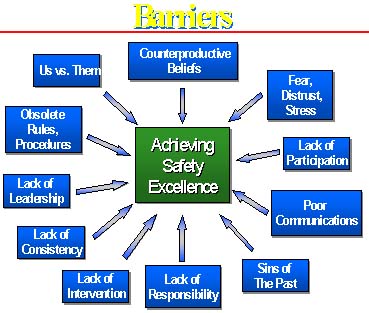
Other barriers to progress include:
- Counterproductive Beliefs: Attitudes like "It won't happen to me," "I've done it this way 1,00 times before," or "We don't have time to do it safely" encourage risk taking.
- Fear, distrust, and stress: Fear of layoffs and increased production pressures lead to an increase tendency to rush and ignore safety procedures, as well as stress levels that produce inattention, fatigue, and loss of focus.
- Lack of participation: Employees may be resistant to participate if their attitudes don't reflect the value or benefit to themselves and others. Past attempts to make a difference with no results can inhibit people's willingness to try again.
- Poor communication: Employees who do not inform co-workers when they are about to engage in a hazardous activity present a real threat. For example, a craft worker enters a tank alone and fails to notify a co-worker or supervisor or a change in safety policy/procedure does not "make it down the line." Upper management's' message and commitment can break down with communication ineffectiveness.
- Lack of management support: Although management claims that "people are our most important product, " management's lack of presence on the production floor and lack of funding for safety projects sends the opposite message.
- Sins of the past: Line and management employees often feel discouraged about trying new approaches to safety, health, and environmental improvement because of past events. For example, management decisions that were unfavorable to employees in the past, such as wage and benefit cuts, or a lack of support for suggestions for improvement, can hamper involvement in the present.
- Lack of responsibility: Employees who believe that their safety is the responsibility of someone else will be less likely to be accountable for their own safety or to take steps to learn safer habits.
- Lack of intervention: Many hourly employees, supervisors, and managers hesitate to intervene when they observe another employee's unsafe behavior. This is usually due to a fear of the other person's response.
- Lack of consistency: One week, a supervisor is intent on production at any cost, but at a prior week's safety meeting, she/he stated that safety was the company's top priority. A lack of alignment in actions by all managers and supervisors can create the perception that safety, health, and the environment are not taken seriously.
- Lack of leadership: When supervisors and managers fail to provide proper direction to achieve safety, health and environmental objectives, wear PPE, or follow safe operating procedures, they loose credibility as a role model.
- Obsolete rules and procedures: If rules are unclear, outdated, or inappropriate, employees tend to ignore them, finding ways around the requirements.
- Us versus Them: Unresolved past conflicts combined with current stresses are a powerful force that can encourage noncompliance.
Back to top
Involve all levels of the organization
William James, a noted philosopher and psychologist, said, "The greatest discovery of my generation is that a human being can alter his or her life by altering his or her attitude." Trying to change any employee's behavior by focusing solely on behavior will produce limited results and success. Changing behavior by changing employee attitudes requires overcoming the basic human resistance to change. For most of us, we are more comfortable with the status quo.
In order for a culture change to be effective, it needs to impact all levels of the organization. Leave no one out because the group that you leave out will anchor your culture to the old way of doing things and impede the culture change to excellence in safety, health, and environmental performance.
An effective attitudinal and behavioral; improvement process involves all levels of the organization in creating and aligning behind a common safety, health and environmental vision:
- The self-management level.
- The peer/team support level.
- The leadership level, including managers, supervisors and line/union leaders.
- The organizational level, including the culture, the norms, values, beliefs, attitudes, systems, and commitments of the company and its employees.
Back to top
The following steps have proven to produce breakthrough results in preventing accidents, injuries, environmental incidents, and in reducing workers' compensation costs:
- Step 1- Assess: Survey the culture to determine prevailing attitudes, beliefs, and behaviors related to safety, health and the environment by way of confidential questionnaires, interviews and focus group meetings.
- Step 2 – Train All Employees: Training that focus on what causes people to become distracted, to take risks, or to act unsafely, even when they know what they should do is essential. It also should address the underlying, "human mechanisms," that cause people to place themselves at risk. Specific skills should include self-observation, self-management, and interpersonal skills. Leaders must be trained in leadership, communication, empowerment, behavior change, coaching and counseling skills.
- Step 3 – Involve Employees: Leave no one out. Greater participation results in grater ownership, which leads to increased conformance. Using a structured problem solving process that identifies rules, policies, procedures, equipment, and processes that need fixing focuses the organization on continual improvement. Then having labor and management work together to make timely repairs and corrections creates cooperation, alignment and support.
- Step 4 – Reinforce: Ongoing training for all employees reinforces key concepts.
- Step 5 – Offer Ongoing Support: Ongoing support is needed to sustain the process and keep it on track.
- Step 6- Customized observation and Review: Line employees, supervisors, and managers work together to develop meaningful processes for observation and feedback, support, and empowerment, as well as activity measures.
Resulting cultural changes also help carry the process forward, and create other lasting and positive changes. Chief among these are improved attitudes, increased trust, better communication, and increased participation, which boost quality, productivity, and morale. Employees perceive – rightly – that they are respected that their input carries weight, and that they have more control over their own destiny. They have more trust in management and fewer grievances.
Back to top
Results from an effective behavioral safety, health and environmental improvement process are consistent in all parts of the country, across a variety of industries and employee groups. Short-term results (months 1-4) include changes in personal attitudes and beliefs which lead to greater use of protective gear, improved compliance with regulations, increased cooperation and willingness to give and receive corrective feedback, resolution of long-standing safety concerns, and greater responsiveness and support from supervisors and managers.
Mid-term results (months 5-12) include significant reductions in injuries. Recordable and lost time injuries drop an average of 55 percent and 78 percent respectively. Cultural change is in progress – clients report better relationships among all personnel, and more support for members of the organization. Over the long-term (13 –60 months), statistics tell the story and solid cultural changes herald a permanent transformation in individual and group response.
- A pharmaceutical company of nearly 410 employees reduced its total number of incidents by 99% over a 5-year period.
- An applied R & D facility in the chemical industry with 374 employees reduced recordable incidents and lost time accidents over four years down to zero injuries.
- A petrochemical company with 440 employees dropped its number of unsafe incidents from a 0.8 OSHA rate to a 0.3 rate over three years.
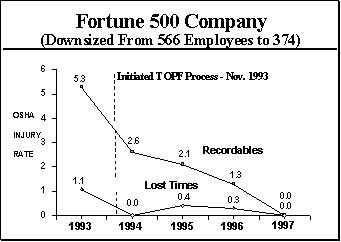
Forward-looking employers are unequivocal in their belief that safety, health, and environmental responsibility must become fully integrated with other business processes. The behavioral safety approach holds that attitudes and behaviors that lead line employees, supervisors and managers to "do the right thing," when it comes to safety, health, and environmental performance are precisely those that lead them to succeed in other arenas at work and at home. The process promotes organizational as well as personal well being.
About the author: Donald H. Theune is vice president of The Topf Organization, 3000 Valley Forge Circle, Suite G-15, King of Prussia, PA. He can be reached at telephone: 610-783-1776 or via e-mail at Dtheune@topforg.com.
Back to top